Philosophy
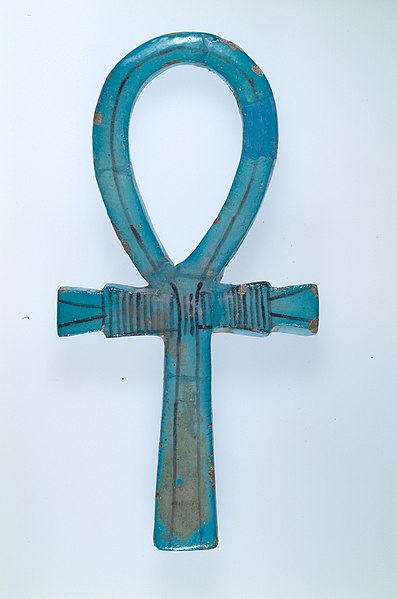
There have to be as many philosophies on designing pinball machines, as there are pinball machine designs.
Contents
We're Building A Pinball Machine.
— Us1
1 I don't know what came over us.
~ Humour ~
Sometimes people do foolish things. "Let's build a pinball machine". I don't remember saying it, or what prompted it (probably Pinfest 2022). But I said it, and Miranda enthusiastically agreed. A year later and things are well underway, or at least well started?
The project plan has around 90 million things left to do, and a completion date of August 2025.
Achievable? Yes2
2 Maybe.
The Way of Pinball Construction
We could:
- Re-theme an existing machine.
- Re-theme and reprogramme an existing machine.
- Build everything from scratch, including mechanisms.
- Buy new or new-old-stock parts, and assemble from scratch.
- etc.
There are also different design approaches to the doing of the build:
- Organic, just start building - this always ends well (not).
- Design, then build - the designs always work-first-time (not).
- Design, build, redesign, and rebuild - sounds nice and quick (not).
Miranda is an artist, I'm an engineer and an artist on-the-side...
It quickly became apparent that we had some strong views. Miranda was not in love with modern pinball art. She loves the game, the fun of the game, and the sculptural elements found in some games.
I want robust functioning mechanisms, elegant software, and an artistic design that supports the machine's functions.
Overarching Goals
These are the goals for the entire project, from trips to the shops through to the final glass polish. I soon discovered that objective one is unattainable for lots of jobs.
Must:
- Be fun to build.
- Be capable of mass production.
- Follow the 3 Rs, Reuse, Repurpose, Recycle - especially for the prototype.
- Economy. Help more people build pinball machines by finding a way to reduce component cost. I want to use Commercial Off The Shelf (COTS) components at best advantage (cheapest).
Goals for Final Build
These are the goals for the final machine itself. They seem simple. As things move along it becomes obvious they are not.
Must:
- Play like a real machine and also be fun to play.
- Look attractive and unique.
- Be simple to play and have objectives that are always clear.
Constraints for Final Build
These are real-world limitations that impact on our ability to make pinball machines...
Must - be constructible with "ordinary" tools and equipment, the things someone setting out to build a pinball machine should have or reasonably expect to buy. Nothing fancy, so:
- Power tools:
- router.
- jigsaw.
- sander.
- 3d printer.
- Rotary tool.
- Craft plotter / Die-cutter machine.
What do these Goals and Constraints mean in real terms?
Some of these have early effects on the build, and some much later. I'll start with the ones that impacted right from the start.
Be fun to build means minimising woodwork. I can do it, but don't enjoy it so much. So buy a cabinet and fix it up. It also means minimising playfield routing and drilling, which results in non-standard component choices.
I'm a fixer, and I'm not comfortable consuming a repairable pinball machine for parts. The Reuse, Repurpose, Recycle goal (we dislike waste), and the Economy goal means we want to source components from a condemned machine; and bolster these mechanisms with new mechanisms as needed.
Economy also factors greatly in the control system decisions later...
Mass production we don't want to make pinball machines for profit (or loss). I value maintainability, and keeping an eye to using parts with long-term availability and/or ease of manufacture and suitable pricing means that it will be easier to keep the machine operating.
Look attractive and unique means a coherent colourway and design elements. My partner is an artist, and a resin artist to boot. Incorporating bespoke resin elements for embellishments and playfield mechanisms is a major opportunity. This also rules out a re-theme for us. We may only make one machine so we want it to be a showcase.
Ordinary tools and equipment I'd love a CNC machine, but they are expensive, and judging by the online videos, neither easy to set up for precision work, nor to get the milling design right. Outsourcing is expensive, and my local maker groups aren't certain what CNC is, so that's not much help :-) So for us, CNC is out.
The 3d printer is for making parts for testing, and in some cases, for the final build. I'm using a cheap-but-well-adjusted filament printer with PLA for testing and PETG for finals.
The craft plotter will make stencils for artwork and inset symbols.
The choice of tools, parts and equipment also means we will design, and build, and redesign, and rebuild; moving from part to part and job to job...
Initial Project Design
The initial design was very promising.
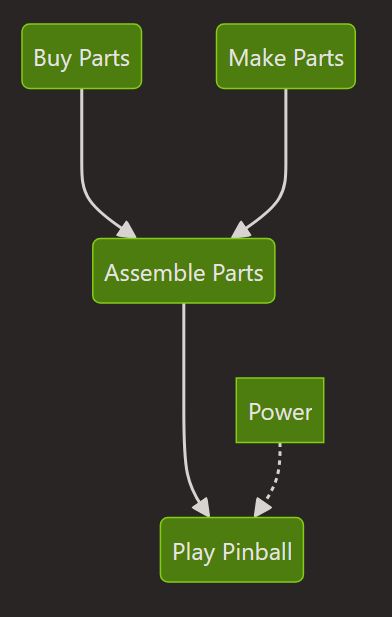
It got a little more complicated after a brief thinking-about.
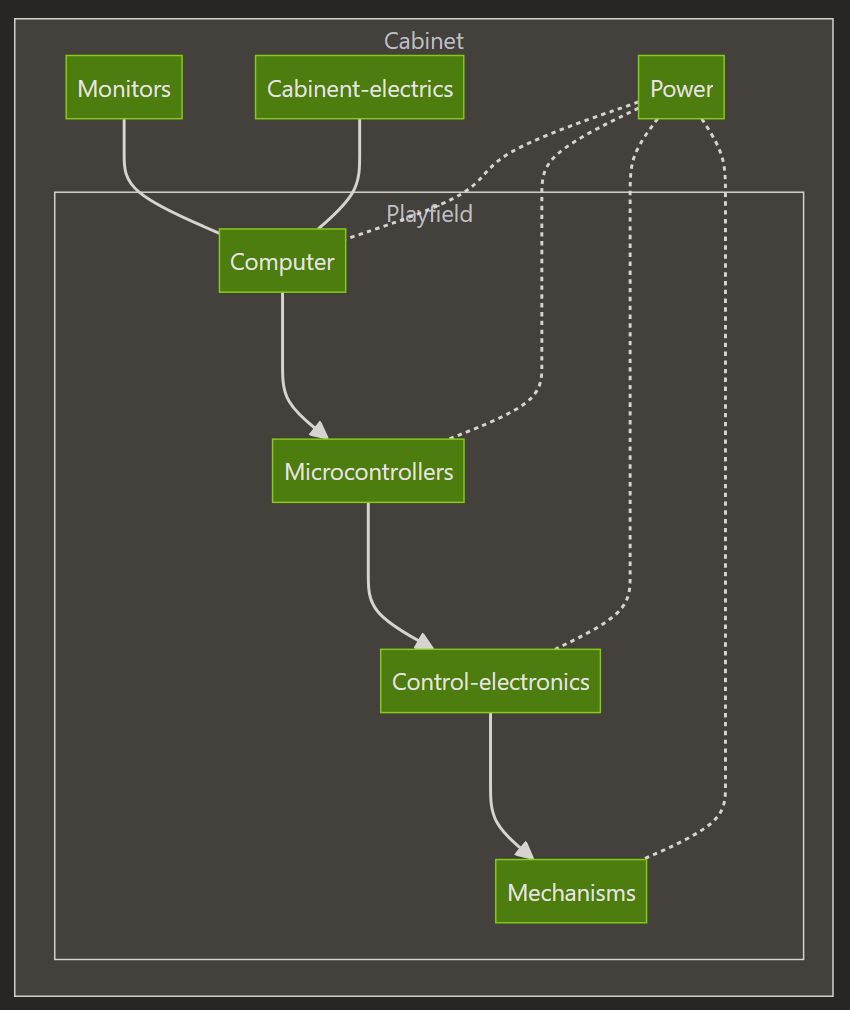
The computer communicates with the microcontrollers, which in turn signal the control electronics which in turn drive the playfield mechanisms.
The computer also controls multimedia - scores, video, music and sound.
The initial design has the control computer attached to the playfield.
This to keep the wiring harness short and minimise connections between the playfield and the cabinet.
Cost saving and electrical noise immunity being the main goals.
And so it began...
Grrrr.
— Anubis3
3 The above quote is excerpted from a presentation by Anubis on The Morality of Tomb Raiders.